“Continuous improvement is at the heart of our development strategy, Kaizen is a Culture, a state of mind for my co-workers.” Mr. Khaled Daami, General Manager Eleonetech.
What is Kaizen?
First practiced in Japan after World War II and most notably known as part of THE TOYOTA WAY, KAIZEN is simply the Japanese word for IMPROVEMENT or change for the better.
The Kaizen concept is a way to approach Manufacturing, Engineering, Management and beyond. It applies to Business processes such as purchasing, logistics, supply chain…
Kaizen refers to activities aiming a continuous improvement of all functions and attempting to eliminate waste. It involve everyone in the company, from the assembly line workers all the way up to the CEO. By means of standardizing activities and improving upon evaluating current practices, organizations and businesses are willing to change for better.
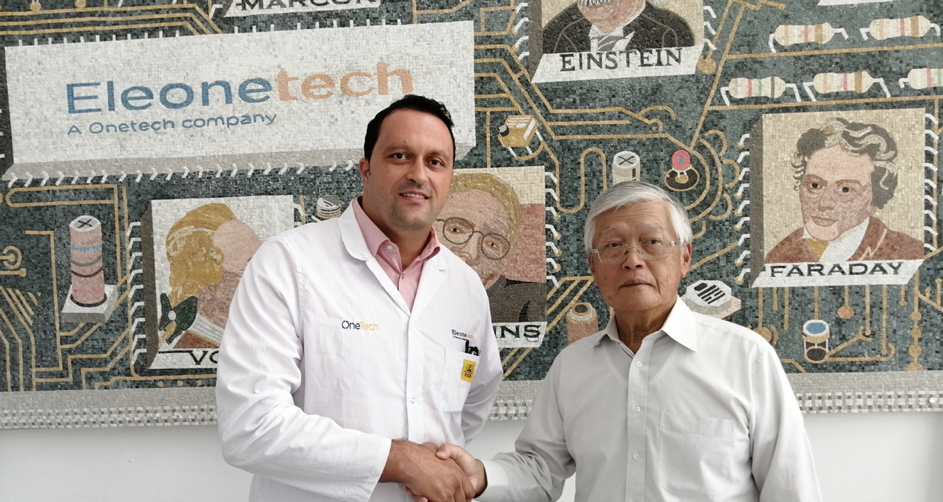
Kaizen Project by the JICA in collaboration with the CETIME
As part of The Tunisian-Japanese Cooperation Program for a sustainable economy baized on a culture of quality and productivity, the Japan International Cooperation Agency (JICA) and the Ministry of Industry through its Mechanical and Electrical Industries Technical Center (CETIME) launched THE KAIZEN PROJECT.
In competition with five other Mechatronics companies, Eleonetech has accomplished the best improvement rate and therefore has been invited to present its achievements during the Closing Ceremony to be held on 10/10/2019.
How did Eleonetech apply Kaizen ?
The implementation of PLAN, DO, CHECK and ACT (PDCA) has proven to be successful when aiding Eleonetech to improve upon its processes and activities. Besides, Eleonetech has a Lean Manufacturing department dedicated to continuous improvement on a daily basis. The company has been successful in several improvement projects, including:
- The productivity improvement project increasing productivity by 80% thanks to the automation of some manual activities.
- The loading time improvement project was also a success; the loading time of series has been optimized by 81%.
- The store flow optimization project allowed a reduction in the handling time of the raw material between its receipt and the output of production.
- The culture of organization, cleanliness, standardization and monitoring has been a fundamental pillar of the Kaizen project’s success. Indeed, the 5S yard was able to create a real dynamic and a perfect collaboration between departments. A net improvement in the average of the 5S level has been recorded. It went from 42% to 63%.
- The Safety project has meanwhile reduced the number of accidents and absenteeism rate.
0 commentaires