As the coronavirus spread around the world, the electronics supply chain suffered through various component shortages. While the economy is on the fast track to recovery, the aftershocks of the pandemic continue to impact businesses significantly.
Global shortage in semiconductors chips has been steadily worsening since last year and appears to reach crisis point.
According to the Semiconductor Industry Association, global semiconductor sales increased 6.5 percent in 2020, demonstrating a rapidly growing demand for chips from Automakers and Tech Giants. There is a new level of demand that can’t be kept up with.
Although production is back to normal, a new surge in demand driven by changing habits fuelled by the pandemic has emerged. the booming sales of home computers, TVs, new games consoles and 5G mobile phones have all driven demand for semiconductors.
Chips are everything in modern electronics
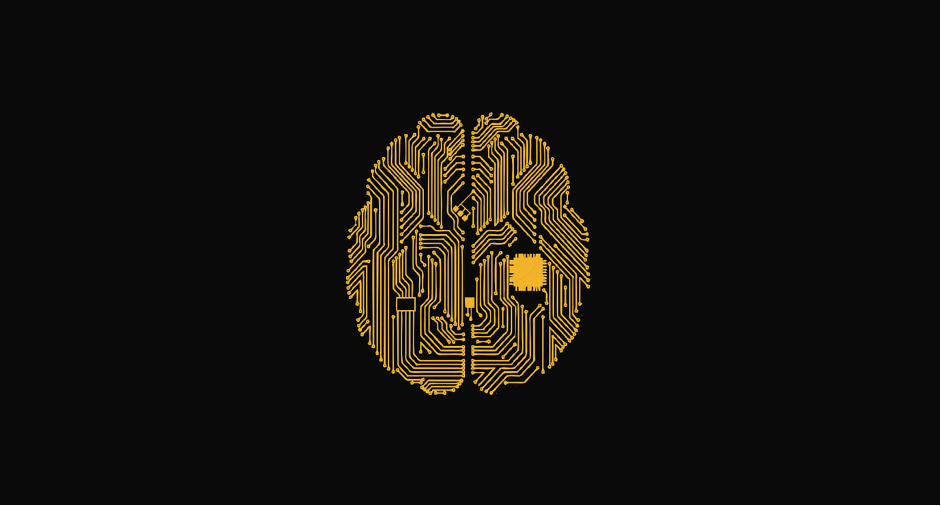
Semiconductors are the brains within every electronic device, enabling highly advanced technologies in healthcare, communications, computing, transportation… and connecting every corner of our lives.
In the automotive space, chips have made cars substantially smarter, safer and more efficient. They are primarily used in advanced vehicles for brakes, power steering, infotainment systems…
The booming demand for electronics, increased competition between Automakers and Tech Giants as this global shortage in semiconductors grows.
In the automotive sphere, the global shortage of certain semiconductors has impacted the market, slowing production of some cars. As it stands, automakers are projected to lose billions of dollars in earnings this year due to a shortage of semiconductor chips.
Last to the party, autos have been the worst affected
Car manufacturers, who cut chip orders as vehicle sales fell last year, found themselves at the back of the queue when they tried to reorder when the market rebounded.
According to CNBC, automakers are scrambling to get supplies of the chips, which have extremely long lead times due to their complexity.
If Apple is spending $56bn a year and the entire global car industry buys about $37bn worth of chips, it’s easy to guess who is getting supplied first.
There is a serious imbalance in the pecking order of who is getting the limited chips first.
OneTech’s Supply chain resiliency program
Benefiting from the trust of our partners and over 24 years of expertise in EMS, we were able to offer alternatives and new options to our customers.
It is essential to ensure that our customers businesses are remaining on track. The flexibility and proactivity of our teams has ensured supply chain’s continuity and reliability.
At OneTech group, our role is to support our customers navigate struggles and to ensure the continuity of the supply chain through people and processes.
The semiconductor chip shortage is manageable and can be capitalized on by developing a flexible workforce model, a reliable network of suppliers and customer involvement.
Act now, think later. Better to discuss material over cost than to discuss line stop.
Covid-19 has required supply chain changes. As part of our strategic adjustment, we have developed a supply chain resilience program. The top focus areas are responding to disruption and reducing risk.
First of all, we focused on what can be controlled and optimized; we have:
- strengthened our team and doubled our workforce
- intensified relationships with our partners
- adjusted sourcing partnerships and revising approved vendor lists
- expanded our network of providers and broadened actively our research
- effectively assess new suppliers
- optimized our processes to streamline response times to process recovery
- had to quickly identify new options for international shipping
The lead time for high-end semiconductors, which is usually long, doubled from 18 weeks to 36 weeks and even further. Passively waiting for semiconductors production to resume is not a viable option if we are to keep SOPs on time.
Our teams were able to offer alternatives to BOMs depending on the availability and lead times since some electronics components remain scarce on the market.
Full re-design options have been also suggested to customer through our R&D department.
In addition, we are working on our ability to predict shifts in the supply chain to proactively respond to it. We keep a constant watch on lead-times of multiple electronic components to acquire visibility into coming changes and easily adapt.
If there is something to remember is that supply chains are volatile but still manageable; you just need the right EMS partner.
0 commentaires